14 Component–Component Interfaces
A seemingly endless variety of implant components may be affixed to one another via a multitude of techniques. In this chapter, these components are defined, and the mechanisms by which they are attached to one another are subsequently described. An implant is a device used to stabilize the spine via the connection of two or more spine components (segments). A construct is the combination of the implant and the spine segments encompassed by the implant. An assembly is the collection of components that together make up the implant. A longitudinal member (e.g., rod, plate) connects two or more anchors. An anchor (e.g., screw, wire, hook) affixes to the bone and to the longitudinal member. A cross fixator affixes two (usually parallel) longitudinal members to each other. The mechanism by which longitudinal members, anchors, and cross fixators are affixed to one another is the topic of this chapter.
The locking mechanism used between the components of a spinal implant system (construct) is essential for the establishment of construct integrity. For the most part, two types of longitudinal members are used clinically: rods and plates. The longitudinal member is connected to other implant components by one or more of the seven commonly used fundamental types of locking mechanisms: (1) three-point shear clamps; (2) lock screw connectors; (3) circumferential grip connectors; (4) constrained bolt–plate connectors; (5) constrained screw–plate connectors; (6) semiconstrained screw–plate connectors; and (7) semiconstrained component–rod connectors (Fig. 14.1). Usually, a combination of two of these locking mechanisms, working in opposition to each other, is used at each component–component interface. This provides a pincer-like action to grip the rod or plate on opposite sides. For example, a circumferential grip connector may be used with a lock screw connector at opposing sides of a rod (Fig. 14.2). Such use of a combination of strategies is undertaken by modern day polyaxial screw–rod connection mechanisms. These connection mechanisms engage the screw head with the rod, usually via a three-point shear clamp mechanism applied by the locking screw to the rod. This causes the rod to engage the base of the head in such a manner that the position of the polyaxial screw head becomes fixed in three-dimensional space. Interface friction may be enhanced with knurled surfaces, which allow the seating of lock screws (e.g., Cotrel-Dubousset), or with a grid-on-grid surface (see the following).


Constrained (rigid) screw–plate interfaces, such as constrained bolt–plate connectors (e.g., fixed moment arm cantilever beam connections, which were initially employed by the Steffee plate in the 1990s), generally are stronger than most hook–rod or hook–screw interfaces. Other factors, however, must be considered during the implant selection process.
14.1 Methods of Assessing Component–Component Interfaces
All types of locking mechanisms rely on friction between the components to minimize or prevent failure at the component–component interface. Therefore, implant surface characteristics are a critical aspect of component–component interface considerations. Compatibility (or lack thereof) between the surfaces of the interfacing components is also a critical consideration. Some component–component interfaces rely mainly on torque or other forces applied; others rely more on friction between the components to secure the desired interface integrity. All, however, rely on both to one degree or another. Component–component interfaces are commonly assessed with the American Society for the Testing of Materials (ASTM) criteria.1
Mechanically, several laboratory techniques can be used to assess component–component interface integrity. These include (1) axial push strength and (2) torsional strength (Fig. 14.3), which are the most widely used and the most easily reproduced.

14.2 Locking Mechanisms
14.2.1 Three-Point Shear Clamp
The three-point shear clamp provides significant resistance to the application of axial, torsional, and bending moment forces. It relies primarily on the force applied at the interface and secondarily on the friction between components. Security is attained via the application of torque to a nut (bolt–plate connector) or a tangentially oriented lock screw. This closely approximates the rod to two contoured surfaces (circumferential grip connectors). These combinations provide both halves of the pincer mechanism required for the attainment of security (Fig. 14.4). This is accomplished via a three-point bending-like mechanism (see Chapter 17).

14.2.2 Lock Screw Connectors
A lock screw connector uses a set screw mechanism to appose the rod to the other half of the component system. Thus, it provides half of the pincer mechanism required for security. The other half of the pincer mechanism is usually either a three-point shear clamp or a circumferential grip connector. The lock screw may be applied end-on or tangentially. There appears to be a mechanical advantage to tangential application. The lock screw may be seated on a knurled surface, relying mainly on friction between the two objects, or on a smoother surface, relying mainly on a circumferential gripping force (Fig. 14.5a) and slight component deformation. An end-on lock screw design also allows the application of a three-point bending-like complex of forces (Fig. 14.6b). The lock screw design is stiffer than most other fixator connections.2,3 This may be in part related to the rigid fixed cantilever beam characteristics of these systems, more so than the component–component connector strategy.

14.2.3 Circumferential Grip Connectors
Circumferential grip connectors may be used to provide both halves of the pincer circumferential force application or, more commonly, only half of the pincer, as with a lock screw. Representative examples are depicted in Fig. 14.6.

14.2.4 Constrained Bolt–Plate Connectors
The terms constrained, semiconstrained, rigid, dynamic, and semirigid describe different spinal implants qualitatively (seeChapter 16). They can be used to qualitatively portray and define component–component interfaces, as well. Constrained (rigid) interfaces are stiff and do not yield, except on failure (i.e., fixed moment arm cantilever beam fixation). Semiconstrained (dynamic or semirigid) interfaces are less stiff and allow some movement at the component–component interface and between spinal segments.
Constrained (rigid) bolt–plate connectors are applicable to screw–plate systems, as well as to hook–rod or screw–rod systems (Fig. 14.7a).

Constrained bolt–plate connectors are very rigid and the strongest connectors available. This is particularly true at screw–plate or bolt–plate interfaces. Component–rod interfaces are, by their nature, slightly weaker. Rod implant–implant connections that use a bolt–plate mechanism of connection generally provide greater interface security than those that do not. The tangential lock screw mechanism of security attainment, which provides a stronger implant–implant interface than the traditional eyebolt mechanism, may provide further biomechanical advantages. This implies that rod-to-implant interfaces that mimic a bolt–plate connector (three-point shear clamp) are stronger than those that do not.
Constrained screw–plate or bolt–plate connectors used with screw–plate systems (e.g., Steffee plate) pose problems of latitude for the surgeon. The screws must be placed in a relatively linear manner, at similar heights and in similar orientations. Furthermore, they are usually bulkier than screw–rod systems. Spacers, washers, and contoured screw hub–plate interfaces have been used to compensate for some of these problems. However, they present additional problems (Fig. 14.7 b–h).
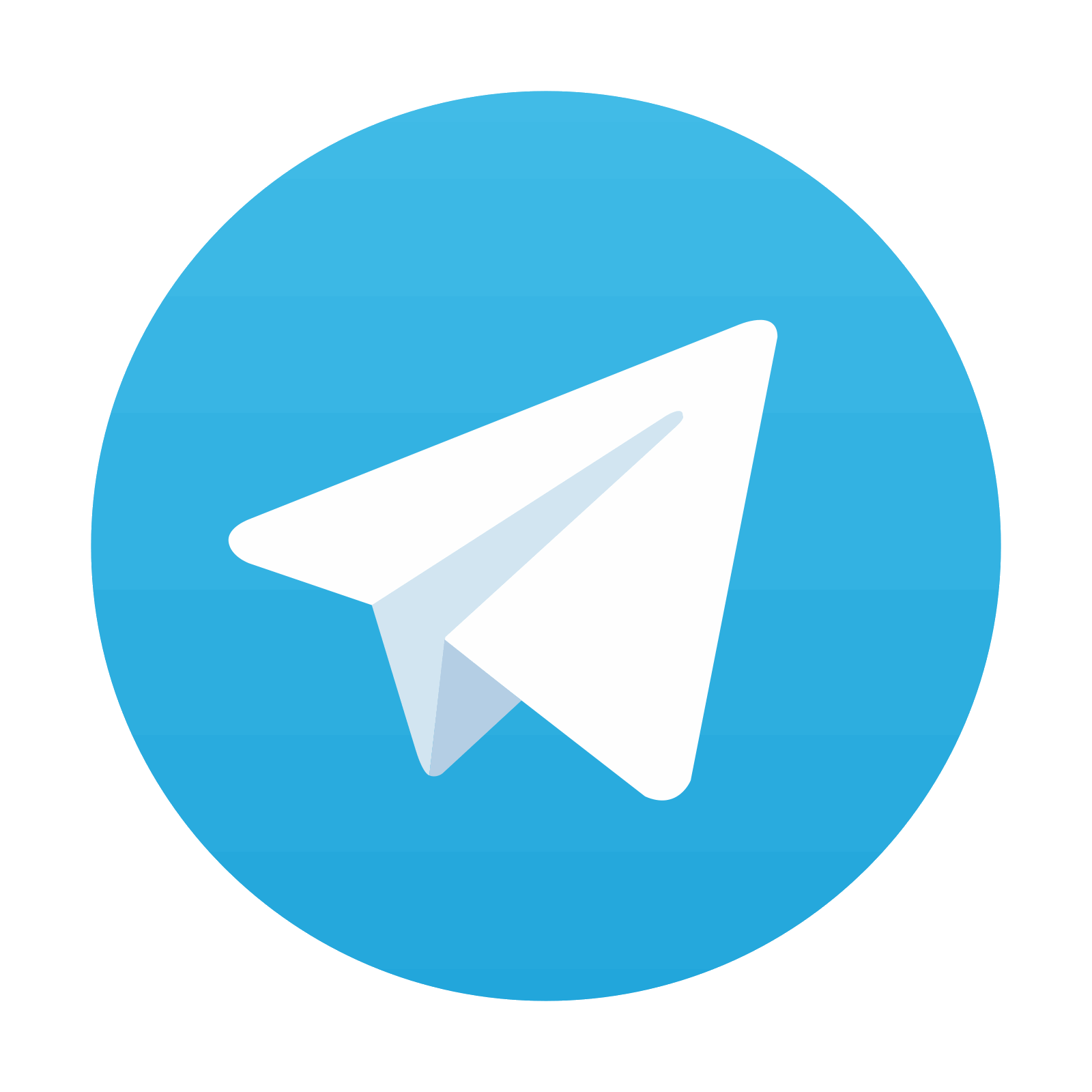
Stay updated, free articles. Join our Telegram channel
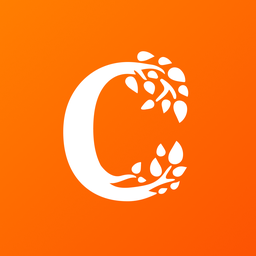
Full access? Get Clinical Tree
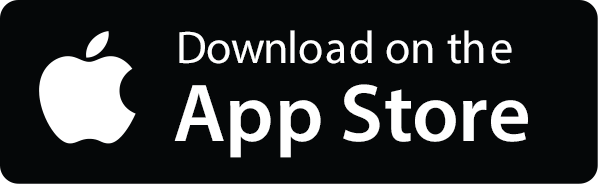

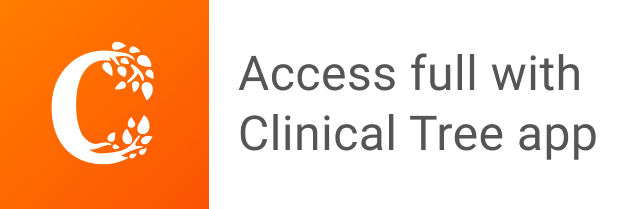