7 Supervisory-Controlled Robotics
Abstract:
Supervisory-controlled robotics involves a semiautomated process executed by a robotic application that is actively supervised by a human operator. It is derived from supervisory-controlled theory and has been widely applied in vehicular and infrastructural processes prior to its introduction to surgery. Supervisory-controlled robotics in surgery involves the combination of process control and vehicle control into a manipulator system. It generally involves three stages: planning, registration, and navigation. Planning involves image acquisition, registration applies this to the surgical field, and navigation involves executing the physical work of performing the procedure. Various iterations of supervisory-controlled systems have been developed for surgery. The applications for spine surgery have mainly involved assisting in spinal instrumentation. Future developments are aimed toward safer and less invasive execution of other components of procedures such as decompression. The potential advantages of supervisory systems are improved precision and a less invasive approach. Potential pitfalls are failing to recognize errors in data interpretation and execution, especially between registration and execution stages. While future applications of robotic surgery may eventually seek full automation, supervisory-controlled systems offer precision and improved and less invasive surgical trajectories while having the safety of human supervision.
7.1 Introduction
In medicine, robotic applications are generally divided into three different categories. 1 The first is shared control systems, where the surgeon provides the input and guidance for actions as the robot gives feedback and input on the actions, usually in the form of movement enhancement or stabilization. The second is the telesurgery system where the surgeon remotely controls the robot movements as in the da Vinci surgical system. The third is the supervisory-controlled robotic systems, which are the focus of this chapter.
7.2 Supervisory-Controlled Theory
Supervisory-controlled robotics is derived from supervisory-controlled theory, 2 which in general takes two forms. One is where an automated process is directly supervised by human control and, when needed, has its algorithm modified to better meet the needs of the operator’s goals. The alternative form involves a preprogrammed machine process, which completes a smaller task, provides feedback on the result, and then awaits further instructions from a human operator in how to proceed. Essentially, it is a process in which the human operator, on a continuous basis, is programming (i.e., instructing) the robot, which in turn continuously relays information back regarding the operating environment. In one respect, it takes a step back from a fully automated environment that requires the ability to sense and respond to every possible combination of problems and challenges that can arise. The supervisory system instead leaves any problems that arise during the automated process to the human operator to respond to and solve.
Supervisory control has been a dominant element in process control and vehicle control for over half a century, playing major roles in improving safety, efficacy, and overall capabilities in several sectors of industry and infrastructure. 2 Process control is integral to the operations of power plants and water management systems to name a few large-scale processes. Vehicle control has had a large role in aerospace systems, underwater exploration, and industrial manufacturing with famous examples including the Apollo spacecraft, modern air traffic control, and underwater submarines. More pertinent to robotic surgery, however, is the combination of process and vehicle control into a manipulator system such as a robotic arm or display system that expands the human operator’s capabilities.
The manipulator system application of a supervisory-controlled system is what underlies the modern robotic surgery system. Compared to an assembly line system, where each task is predetermined, applications requiring supervisory control of manipulators consist of unpredictable tasks and environments. The human operator (i.e., surgeon) must program the manipulator (i.e., robot) in order to deal with each new situation. This may even include merely initiating predetermined tasks at the correct time.
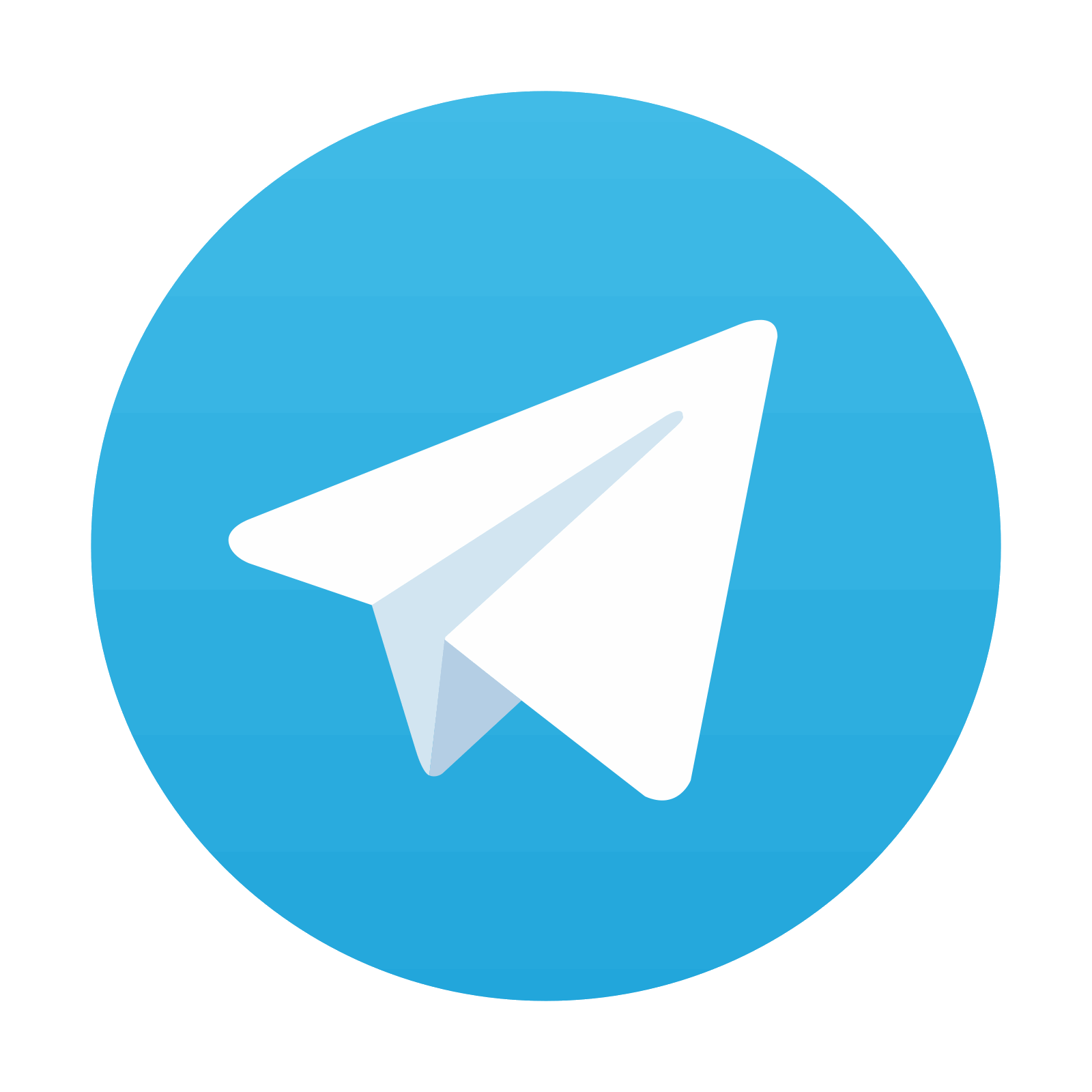
Stay updated, free articles. Join our Telegram channel
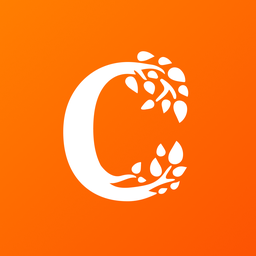
Full access? Get Clinical Tree
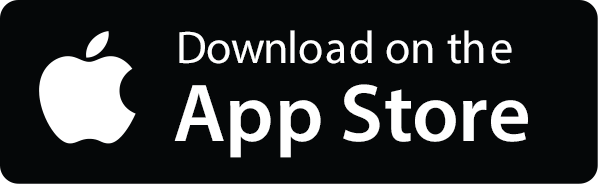
