General Principles of Spinal Wire and Cable Fixation
This chapter reviews the fundamental principles for successful fixation with wires and cables as they apply to cervical and occipitocervical stabilization. Wires have diverse uses, are simple to apply, and are familiar to most surgeons. They create a mechanical tension band for the posterior cervical spine. They can be used to attach adjacent vertebral surfaces together, or they can be used to bind bone grafts or metal implants to the surface of the occiput and posterior cervical spine. Wires also can be attached directly to several adjacent motion segments to achieve multiplanar control of segmental motion.
The spinous processes, the laminae, the facets, or the occiput can serve as points of bony attachments for wire. The goal of wiring is to fixate the spine until a solid bone fusion develops.
Techniques of Wire Application
There are several different types of wires available for surgical use. Monofilament wire, double-stranded, twisted wire, or braided wire cables are used for cervical or occipital fixation.
Traditionally, monofilament stainless steel has been the most common wire used for spinal fixation. Monofilament wire is available in a variety of diameters ( Table 36.1 ). For the cervical spine, 20-gauge wire is the most convenient; it is easy to work with and relatively strong. In comparison, 18-gauge wire is stronger than 20-gauge wire, but it is stiff and therefore difficult to twist, contour, and manipulate. Twenty-two-gauge wire is more flexible than 20-gauge wire, but it is weaker and more likely to fatigue and break. Usually, 20-gauge monofilament wire is used to fixate the occiput, spinous processes, or cervical laminae. Bone grafts or the cervical facets are fixated with either 20- or 22-gauge wire. These applications are modified depending on the individual circumstances.
Modified from Dickman CA, Sonntag VKH. Wire fixation for the cervical spine: biomechanical principles and surgical techniques. BNI Quarterly 1993;9(4):2–16.
Double-stranded twisted monofilament wire has mechanical advantages over single-stranded monofilament wire. Taitsman and colleagues demonstrated that double-stranded, 24-gauge twisted wire is much stronger than monofilament 24-gauge wire. The tensile strength increases up to 8 turns/inch (2.5 turns/cm) and decreases thereafter.1 Double-stranded wires can be prepared easily using a hand drill or a “Robinson” wire twister. The end of a pair of wires is held by the wire twister or is inserted into the shaft of the twist drill. The free ends of the wires are held with a Kocher clamp. The wires are pulled taut and twisted uniformly by rotating the twist drill or the wire twister. A ruler is used to measure the number of twists in the wire.
The preferred method of fixating monofilament wire to the spine is by twisting the wire. A loop of wire is wrapped around a bone surface. The free ends of the wire are brought together; they are crossed and twisted to remove slack from the loop of wire around the bone surfaces. Twisting sets progressive tension in the wire. Wire can be twisted with a needle holder or with a Robinson wire twister ( Fig. 36.1 ). The free ends of the wires are crossed, and one or two twists are placed in the wire. The intersection of the wires is grasped with a wire twister. The wires are pulled upward to distribute tension uniformly in the wire and to remove slack from the wire while it is twisted. Although stiff, the monofilament wires are malleable and retain the twisted configuration permanently. Wires should not be over-twisted or they will weaken and break. Wire also should not be overtightened or it will pull through soft, osteoporotic bone.



Single-stranded or double-stranded monofilament wire usually is twisted at one site to remove slack from the wire. Alternatively, the wire can be twisted bilaterally to distribute the tension in the wire more evenly ( Fig. 36.2 ).
The twists should be uniform. Excessive twisting will change the color of the wire and secondary turns will appear. Kinking of the wire must be avoided when wires are bent, passed, or tightened. Wire should not be kinked, notched, or bent in an acute angle. Acute angles or excessive twisting in the wire make it extremely susceptible to fatigue and breakage.
Braided Cables
“Wire rope” has been used extensively in mechanical engineering in the construction of bridges, elevators, and heavy machinery, among other things. Wire rope consists of several cable strands laid vertically about a metallic or nonmetallic core ( Fig. 36.3 ). Such ropes are very flexible yet strong and resist crushing and distortion. Multistranded braided wire cables were developed as an adaptation of this concept for spine surgery.2,3 Wire cables for spinal fixation were developed by a surgeon, Dr. Matthew Songer, and his father, Robert Songer, an engineer.2 Cables are stronger, more flexible, and more fatigue-resistant than monofilament wire; however, they also cost considerably more. Within the past few years, wire cables have almost completely replaced monofilament wires for spinal fixation. Because the cables are flexible, the risk of neurological injury during wire placement or wire removal is reduced. Wire cables conform to the surface of the laminae. The flexibility allows an even distribution of tension in the cable. Several types of braided cables are marketed for use in spinal fixation. Two representative types of cables ( Table 36.2 ) are discussed later.
Danek Cables
Danek cables (Sofamor, Memphis, TN) are braided wires that are attached to a stiff monofilament leader wire for sublaminar passage. There are 49 wire strands in each cable, arranged in a 7 × 7 array. The cables are composed of titanium or stainless steel.2,3 Single cables or two cables are welded to each leader wire; the double cables are used for sublaminar wire passage. A crimping cylinder is welded to the distal end of the cables. The end of the cable is passed through the cylinder to create a loop. After slack is removed from the cable, the crimp is pinched to fixate the cable permanently.
The double cables have the same crimping mechanism as the single cables ( Fig. 36.4 ). The leader wire is passed through the cylindrical crimp welded on the end of the cable; tension is applied to engage the wire. The crimp is pinched to permanently fix the cable. The cables are permanently, irreversibly secured into position with a metal crimp shaped like a cylinder. The crimp is pinched with a tool that binds it to the cable. Two different tensioner devices are available ( Figs. 36.5 and 36.6 ). The larger combined tensioner and crimper is easiest to use. The tensioner device is used to remove slack from the wire, and a torque wrench is used to adjust the desired wire tension. The desired tension is adjusted using a knob on the base of the torque wrench. The torque measurement is indicated by calibrations, which are marked on the shaft of the torque wrench in inch-pounds and Newton-meters. The torque applied with the wrench is directly proportional to the tension applied to the cable ( Table 36.3 ). The cable is threaded through the crimp, which is held in the jaws of the crimping device. The cable is fed through a locking nut on the end of the crimper. The torque wrench is attached to a locking gear that winds the cable around a post. The torque wrench has a ratchet mechanism that yields when the desired tension is achieved. The crimping device is squeezed until a spring-loaded bar releases, indicating that the crimp is fully pinched. After the crimp is placed, the tensioner and crimper are detached from the cable. The excess cable is cut flush with the crimp.


A smaller cylindrical tensioner, which has a ratchet-driven spring-loaded shaft that tensions the cable, also has been used ( Fig. 36.5 A,B ). The leader wire is threaded through the center of the cylindrical unit, and the cable is locked into position with a lever. A handle on the side of the tensioner is depressed repeatedly against the shaft and released to progressively set the wire tension. A scale on the side of the unit displays the cable tension (in pounds). The crimp is pinched and the cable is cut flush with the end of the crimp.
The ability to set the cable tension precisely is valuable because overtightened cables can pull through weak or osteoporotic bone. A torque of 8 to 12 in-lb is recommended for normal laminae,2,3 and 6 to 8 in-lb are used for facets or weak osteoporotic bone. Table 36.3 displays the relationship between torque and cable tension.4
Danek cables and other wire cables are flexible but should not be bent or kinked. An acute angle weakens the cable and creates a stress riser where the cable can break. The cables are strong under static and dynamic mechanical loading conditions.


Danek cables have a maximum yield strength 2.85 to 2.94 times greater than double 0.05-inch stainless steel wire loops. In fatigue tests, steel cables require 6 to 22 times more cycles to failure than stainless steel wires.4
Titanium cables have failure mechanisms different from steel cables.2 Steel cables are stronger than titanium. Steel cables tend to break under relatively high loads. Titanium cables can fail under high loads because the crimp can slip or the cables can break. In general, we reserve titanium cables for tumor patients or when postoperative magnetic resonance imaging (MRI) is needed. A satisfactory myelogram and computed tomography (CT) scan can still be obtained with steel cables present.
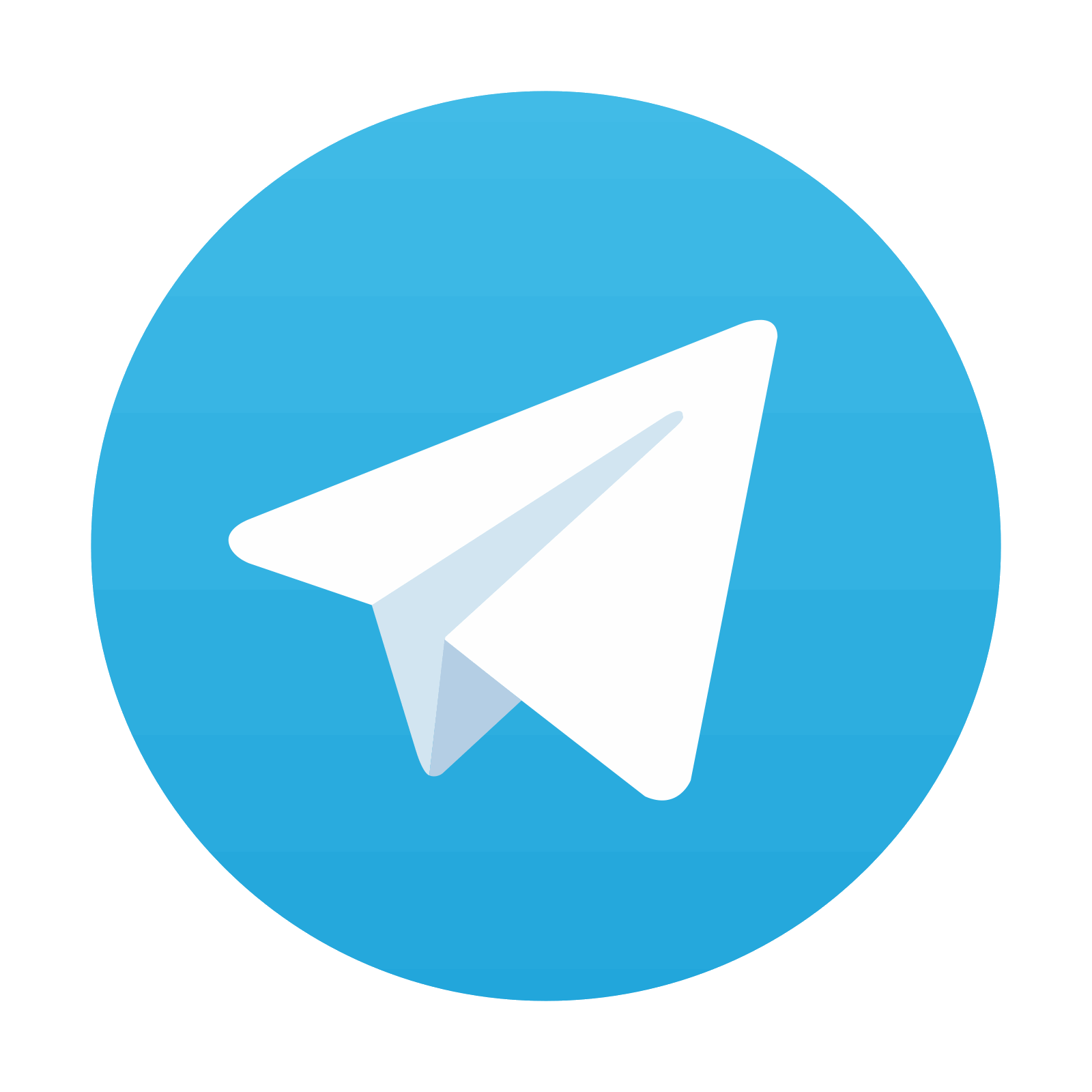
Stay updated, free articles. Join our Telegram channel
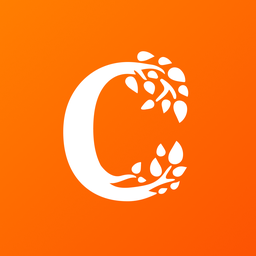
Full access? Get Clinical Tree
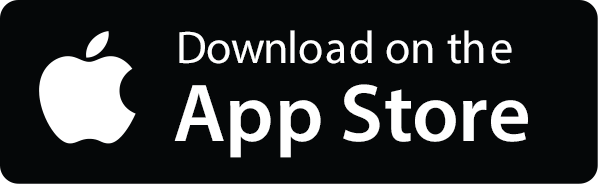

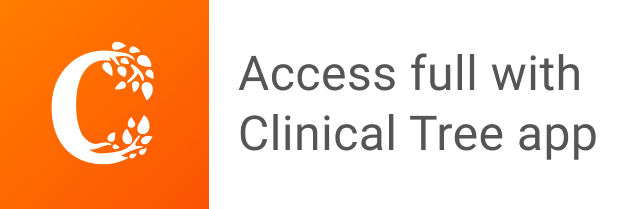