Define
Inputs from customers, stakeholders, frontline workers, and external sources (e.g., research literature, accrediting agencies, payers) prompt a laser-like focus to identify the scope of the real problem
Measure
Data replace assumptions, impressions, and guesswork and establish the baseline performance of the existing system or process
Analyze
Powerful statistics (like Statistical Process Control Charts) optimized for real-time, small N operations improvement problems, identify key root causes and opportunities
Improve
A set of evidence- and data-based improvement actions are implemented and tested to ensure desired outcomes without unintended consequences or suboptimization of other parts of care delivery system
Control
Standard work specifications that operationally define the new optimized delivery process(es), measurement specifications defining process performance, and action steps for process owners to maintain (“hardwire”) the new system over time
Lean
Operations improvement philosophy that emphasizes the creation of value for the customer through the reduction of waste in the process. Waste comes in many forms: defects, overproduction, waiting, neglected talents of staff, transporting materials, inventory, excess movement/motion by staff, and excess handling/processing of materials. It is commonly reported that in a typical organization, up to 30 % of gross revenues are lost to waste [3].
Lean and Six Sigma combine to create high performance by (1) removing wasteful process steps and (2) making those that remain as close to 100 % reliable as possible.
Terminology
- 1.
Voice of Customer
The stated or unstated needs or requirements of the customer (typically the recipient and/or buyer of healthcare services). Can be captured in many ways: interview, survey, observation, and complaints. Understanding the voice of the customer ensures that any process improvement actions are intended to satisfy the recipient, versus the provider, of the service or product. In healthcare, often reflect elements of STEEEP (see below).
- 2.
Voice of Process
A comprehensive understanding of the performance characteristics and capabilities of any process. Best depicted via a graphical Statistical Process Control Chart (see below) that portrays process measurements sequentially over time, with reference to both the central tendency and the normal variation inherent in the process.
- 3.
STEEEP
The six healthcare customer requirements highlighted as paramount by the Institute of Medicine: Safe, Timely, Effective, Efficient, Equitable, Patient Centered [1].
Safe: Avoid injury to patients from the care that is intended to help them
Timely: Reduce waits and harmful delays
Effective: Provide services based on scientific knowledge to all who could benefit and refrain from providing services to those not likely to benefit (avoiding underuse and overuse, respectively)
Efficient: Avoid waste (of time, motion, materials/resources)
Equitable: Provide care that does not vary in quality because of personal characteristics such as gender, ethnicity, geographical location, and socioeconomic status
Patient Centered: Provide care that is respectful of and responsive to individual patient preferences, needs, and values
- 4.
Statistical Process Control (SPC) Chart
A powerful statistical measurement and analytic tool for graphically portraying the performance of a process over time. A plot of time-series data, its central tendency, variation, and statistically derived “control limits” that allow the operator to distinguish normal common cause variation from non-normal special cause variation in the process.
Common cause variation: All processes exhibit common cause variation; it is “noise”—part of the process. It is normal and predictable.
Special cause variation: Some processes exhibit special cause variation. It is “signal”—not part of the process. It is non-normal and unpredictable. Typically reflects changes to manpower, machine, materials, methods, or management [4]. Special cause is detected using three primary empirical rules: (1) Ones (any point outside the control limits), (2) Runs (seven or more consecutive points all above or below the central tendency line), and (3) Trends (seven or more consecutive points moving up or down crossing the central tendency line) [5, 6].
- 5.
Benchmark
An external performance standard or specification against which one’s own process or system can be compared.
- 6.
Healthcare-Acquired Condition (HAC)
Negative patient safety outcomes acquired during the course of receiving healthcare services that reasonably could have been prevented through the application of evidence-based guidelines. The Centers for Medicare and Medicaid Services recognizes the following categories of HAC: surgical site infection, foreign body retained after surgery, air embolism, blood incompatibility, stage III and IV pressure ulcers, falls and trauma, manifestations of poor glycemic control, catheter-associated urinary trait infection (UTI), vascular catheter-associated infection, deep vein thrombosis/pulmonary embolism, and iatrogenic pneumothorax [7].
- 7.
High Reliability Organization
Organization that executes safely and effectively in an environment/demand known to be complex and risk prone. Examples include commercial airlines, nuclear power plants, and military operations. Such organizations are marked by a preoccupation with the potential for failure and a culture of supported communication, teamwork, and learning. Such organizations accept that errors or defects may occur. What is not acceptable is refusal to act on actual or potential errors/defects.Stay updated, free articles. Join our Telegram channel
Full access? Get Clinical Tree
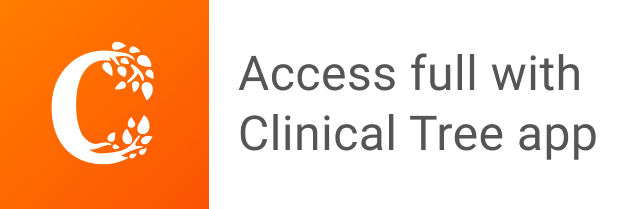