(1)
Department of Neurology, Wake Forest University School of Medicine, Winston-Salem, NC, USA
Abstract
This chapter introduces the reader to lean manufacturing principles. The life and work of W. Edwards Deming, Taiichi Ohno, and creation of Toyota Production System are discussed in detail. There is a detailed discussion of the salient principles of Pull vs. Push, avoiding waste, root cause analysis, the 5 why’s principle, go and see for yourself (Genchi Genbutsu), Jidoka, and introduction to the principles of Kaizen. Case examples and application of these principles are presented.
Keywords
Lean manufacturingToyota Production System (TPS)W. Edwards DemingTaiichi OhnoDeming System of Profound KnowledgeDeming’s 14 principlesJust-in-timeZero inventoryPull vs. pushMudaBanish wasteKanbanJidokaRoot cause analysis5 why’sKaizenAndon boardsAndon cordsPlan-do-study-act cycles (PDSA)Amiodarone toxicityPostradiation REM behavior disorderMyotonic dystrophy 1Myasthenia gravisGranulomatosis with polyangiitis (GPA)Introduction to Lean Manufacturing
A powerful paradigm in manufacturing has been Lean Thinking which has been adopted systematically in many industries with generally good results [1–5]. Lean was pioneered by Toyota Motor Corporation (TMC); it is also referred to as the Toyota Production System (TPS) which is more a philosophy than a set of work practices. Its applications are so universal that it is applied in some form by every major manufacturer whether automobile or otherwise [1–5]. This section will emphasize more on the philosophy and processes behind lean and will avoid approaching it from a “slogan” viewpoint.
Lean has been adopted in healthcare administration to a great extent with many successes. It has started making in-roads into day-to-day bedside healthcare; however, it has not seen the widespread grass roots application among doctors, nurses, and pharmacists which will increase its impact. This section will present a brief overview of Lean followed by application of some important aspects of Lean which can improve dependability in healthcare.
Lean Thinking at its core seeks to eliminate waste and improve quality and reliability. The ideas were pioneered by W. Edwards Deming (1900–1993) and Taiichi Ohno (1912–1990). The work of these two remarkable individuals which started in Japan had the most profound impact on manufacturing across the world since the advent of the industrial revolution.
The Teachings of W. Edwards Deming
W. Edwards Deming was born in Sioux City, IA. He earned his B.S. in engineering from the University of Wyoming in 1921 followed by M.S. and Ph.D. in mathematics and mathematical physics from the University of Colorado and Yale University in 1925 and 1928, respectively. In 1950, Dr. Deming was invited by the Japanese Union of Scientists and Engineers (JUSE), where he delivered a series of lectures entitled “Eight day course on Quality Control.” This seminar had a very important impact on Japanese businesses which adopted his teaching to set benchmarks in quality which helped Japan dominate many industries, especially automobile in the years to come. Dr. Deming donated all the proceeds from the sale of transcripts of his lectures to JUSE. In recognition of his contributions, JUSE instituted the Deming Prize in his honor which is awarded annually to individuals and companies. The Deming Prize for Individuals is awarded to individuals who have made an outstanding contribution to the study of total quality management (TQM) or statistical methods related to TQM. The Deming Application Prize is awarded to companies for making achievements in quality by application of TQM in a designated year [1]. Dr. Deming popularized the Plan-Do-Check-Act cycle (discussed with examples in medical context later). A significant philosophy developed by Dr. Deming is the “Deming System of Profound Knowledge.”
The “Deming System of Profound Knowledge” is as much a personal philosophy as an organizational one. It underscores the importance of individual development for organizational transformation and improvement. The individual seeks and attains a deeper understanding of events, life, and relationships with other people. This transformation leads to profound knowledge where the individual would set an example, be a good listener (but without compromise). The individual would continuously teach others and help others transition from current beliefs and practices towards the new ways of doing things without conflicts or guilt. With this transformation, the individual develops better judgment for his decisions and for the transformation of the organization [2]. Dr. Deming believed all managers must understand the “System of Profound Knowledge” which consists of four intertwined and inseparable parts [2]:
(a)
Appreciation for a system: managers must have intimate knowledge of all processes involving a system such as production, relations with suppliers and customers.
(b)
Knowledge of Variation: understand the nature and causes of variations in quality with understanding of statistical quality control techniques.
(c)
Theory of Knowledge: understanding what is known about processes and what is unknown to develop hypothesis, gaining insight into data to be able to predict and further refine current state of knowledge and understanding, extending understanding by asking questions. “Without theory, experience has no meaning. Without theory, one has no questions to ask. Hence without theory, there is no learning.”
(d)
Psychology: understanding human behavior and interactions.
In Out of the Crisis [3], Dr. Deming advocated 14 principles as ideas for transforming American business.
1.
Create purpose for improvement of products and services.
2.
Being in a new economic age, western management must learn new responsibilities, measure up to the challenge, and demonstrate leadership for change.
3.
Quality is important and must be built into the product in the first place. It should not be dependent on inspection.
4.
Build relations with suppliers, moving towards a single supplier for any one item based on long-term relationships of mutual loyalty and trust. Such an approach minimizes total cost and does not create partnerships based on price tags.
5.
Continuously improve the system of production and service with the end goals of improving quality and productivity. This would improve quality and constantly decrease costs.
6.
Provide opportunities for continuous skill development by instituting training on the job.
7.
Management should encourage leadership. Supervision of production workers and management should be to encourage everyone to do a better job instead of being adversarial.
8.
Create an atmosphere without fear so that everyone can work effectively for the organization.
9.
Integrate departments across the organization by breaking down barriers between them. Research and development, design, sales, and production must work together as a team to foresee and correct problems that maybe encountered during manufacturing or operation of the product or service.
10.
A culture of leadership, ownership can achieve excellence. Slogans, artificial quotas, numerical goals create waste and adversarial relationships and should be eliminated.
11.
The hourly worker should not be robbed of his right to pride of workmanship. The organization, including workers and their supervisors must be dedicated to excellence and quality.
12.
Employees in management and engineering should also not be robbed of their right to pride of workmanship. For this to happen, abolish annual or merit rating and management by objectives.
13.
Create programs for education and self-improvement.
14.
Encourage everyone to work towards accomplishing the transformation. The transformation should be seen as everybody’s responsibility and contribution.
The following sections will show that these principles are timeless.
Taiichi Ohno and the TPS
Taiichi Ohno is widely credited with being the creator of the TPS which is known as Lean manufacturing the world over. Taiicho Ohno, executive vice president at TMC was inspired by eliminating waste in the manufacturing process to improve efficiency, profitability, and productivity at Toyota. History has it that the inspiration for this system struck Mr. Ohno during a visit to a supermarket in the United States. When one product was sold, a replacement was ordered and placed on the shelf. Reordering and restocking therefore was highly driven by sales with customer demand driving what was being stocked and restocked on shelves. The Japanese word for waste is muda; TPS has at its heart the elimination of muda. It is interesting to define waste first so that its elimination can then be better understood [4]. Waste as identified by Mr. Ohno takes several forms—mistakes requiring reworking of finished goods, overproduction of goods with little market demand, steps in manufacture or services that do not add value and slow-down productivity, poor planning of steps in manufacturing which require expensive transport of unfinished goods from one step to the other slowing down the process, poor coordination of intermediate steps in manufacturing leading to downstream workers with little work since upstream processes have not completed in time. Finally, waste involves the delivery of goods or services which do not meet the customer’s requirements or expectations [4]. The above represents the set of identifiable waste in manufacturing, where intermediate steps are well defined. Viewed from this perspective, the reader can only imagine the degree of waste in bureaucracies and healthcare systems. When viewed from this perspective, healthcare is riddled with muda. Detailing all types of muda in healthcare is beyond the scope of this book, but it includes errors in diagnosis and treatment, delays, duplication of effort, expensive laboratory tests and imaging which may not add value to the problem. The interested reader is referred to the work of James Womack, Daniel T. Jones, and Daniel Roos for a comprehensive review of the topic [4, 5].
While eliminating muda is the goal of lean manufacturing, how is this achieved in practice? The major ideas in lean manufacturing which have gone into folklore are the following [6]:
Just-in-Time
Just-in-time is synonymous with TPS. Each process manufactures exactly the same number of items which are used by the next process. This method eliminates manufacture of excessive numbers of intermediates or finished products, where there is no demand. It allows for great flexibility in manufacturing enabling the manufacturer to produce only the right amount of what is needed at the right time. This is the manufacturing equivalent of the supermarket principle observed by Mr. Taiichi Ohno in his visit to the United States. Conceptually, when a customer purchases a red color Toyota Camry in Dallas, TX, an instruction is sent to the production line to build a replacement red Toyota Camry. Carried one step further, orders for component parts such as its engine, transmission; seats (depending on the trim) are placed further upstream in the process. Each step of the manufacturing process manufactures only a small number of parts to replace what was delivered at the end of the line to the customer.
Just-in-time facilitates the development of a “Pull” system. The customer’s action of purchasing a product exerts a “Pull” on the manufacturing system leading to the manufacture of a replacement product. Manufacturing therefore is closely coupled to demand. This is the opposite of the “Push” system, where manufacture of goods or intermediates is performed independent of the level of utilization downstream leading to production or overproduction and inefficient application of resources [4–6]. Just-in-time requires close coordination and communication between manufacturing processes in the assembly line. A typical car today has an inventory of over 30,000 parts many of which are supplied from external vendors. Within the shop floor of the assembly line, a system called kanban is used to link different manufacturing units together. A kanban card is a card attached to a parts bin which contains information such as type of part, its quantity, and other information. When a part is removed from the bin, the associated kanban card is removed and sent upstream to the supplier indicating the part has been utilized. Kanban cards therefore carry information on what parts have been used and where they have been used so that the suppliers can manufacture exactly the same number of replacement parts and deliver it to the required location. The system today is completely electronic but the concept remains the same. This process is not just used by Toyota and its affiliates, but also by external vendors.
Jidoka
Loosely translated means “automation with a human touch.” The origins of the jidoka system lie in the birth of the company itself. Sakichi Toyoda invented the self-powered loom with a built-in capability to stop production whenever thread breakage was detected. This enabled a machine to stop automatically when malfunction was discovered and prevented the manufacture of defective items. This allowed a single worker to be put in-charge of many looms which boosts productivity [6]. This has been refined and extended into the company’s automobile manufacturing business. A single worker can monitor many different machines and processes assisted by modern computer aided visualization tools. When a problem is detected, the production process automatically shuts down to prevent defective parts from being manufactured. The malfunction itself is prominently displayed in production lines using monitors or flashing lights called andon boards which display information about the problem. (Effective data visualization therefore is a powerful tool in this system) When a worker discovers a problem with a particular process, he can pull an andon cord to stop the production line. The jidoka system therefore prevents defective parts from being passed down the assembly line, where they can become increasingly difficult to rectify.
Kaizen
The term kaizen refers to continuous incremental improvement. Kaikaku refers to radical improvement [5]. This requires deep understanding of processes and teamwork between workers and supervisors to refine processes towards gradual improvement. They require close collaborative relationships between workers and team managers and an atmosphere that fosters new ways of doing things and experimenting. Successful corporations devolve responsibility for limited experimentation for improving processes to the grassroots level of the production system. Workers and team managers collaboratively conceive new ways of completing a particular process and are allowed to experiment in a limited manner. Data (processing time, material usage, etc.) from the new method is compared to the old method. If there is significant improvement, the new method is adopted in a more widespread manner throughout the organization; otherwise, it is rejected to move onto the next new idea. Kaizen is intimately connected to the Plan-Do-Check-Act cycle which will be discussed further. Successful implementation of kaizen for any project therefore has teamwork, respect for coworkers implicitly built in.
The 5 Why’s
Taiichi Ohno encouraged the 5 Why’s principle which forms the basis of a very powerful investigative tool called Root Cause Analysis. He encouraged his staff to get to the root of every problem rather than solve the immediate problem on hand. The immediate problem is what is perceived, the deeper problems are the causes of what is perceived and the examiner has to probe deeper into the problem till he gets to the heart or root cause of the problem. In Mr. Ohno’s words “The root cause of any problem is the key to a lasting solution.” He encouraged the principle of genchi genbutsu (“go to the source and get the facts”) which encourages managers to go to the shop floor and see the problem with their own eyes and understand the facts. A connected word in the lean lexicon is Gemba which means “the place” or “market,” where the actual actions occur. When a problem arises in the gemba, managers should go there and understand the genbutsu. This is perhaps one reason for the success of Japanese automakers, while manufacturing problems are understood in reports and solutions proposed by managers in corporate offices in the west, the Japanese system encourages problems to be understood and solved on the shop floor. Taiichi Ohno stressed to his managers to see every problem as a kaizen opportunity. Once the root cause of the problem is understood, processes can be implemented to prevent their recurrence [7].
The following example of malfunction of a welding robot was used by Taiichi Ohno to explain the power of this principle. The first question relates to why did the robot stop? The answer is because a fuse was blown due to circuit overload. The second question is why was the circuit overloaded? This was because there was insufficient lubrication in the bearings. This begs the question why did that happen? Because the oil pump on the robot was not circulating lubricating oil. Why was the oil pump not circulating enough oil? Because the pump’s intake is clogged with metal shavings. Finally, why is the intake clogged with metal shavings? Because there is no filter on the pump. This is the root cause of the problem. The simplicity and power of this method can be readily appreciated from this example. What started as a fuse not working, a seemingly electrical problem can be sourced to the lack of a simple filter in the oil circulation system. A less detailed analysis which asked Why a fewer number of times would miss this solution. The kaizen opportunity here is the design of a filter for the oil circulation system which will prevent this problem from recurring [14].
Implicit in the 5 Why’s or root cause analysis is the requirement for understanding the problem and making a correct formulation to attempt to get to the root cause and attempt a solution. Correct problem formulation is an essential requirement for application of this technique. Root cause analysis is an extremely powerful tool with immense applications in medicine. Of all the TPS principles which were described above, this is perhaps the most important for a physician since it can improve diagnostic accuracy considerably.
Taiichi Ohno’s classic book TPS, Beyond Large-Scale Production is an invaluable textbook about these methods [7]. A criticism of lean has been the less-than-spectacular results when it was applied in the west in many industries. One reason for such a problem is possibly that many corporations attempted its implementation with slogans and catch phrases without encouraging the understanding of processes. Moving towards zero inventory does not necessarily mean successful implementation of TPS. Therefore, problem formulation and understanding of underlying processes is vital to successful application of lean or TPS. A crucial concept to understand is that lean is not a tool-kit, rather it is an operational philosophy which yields results in the appropriate context when applied with deep insight into processes.
Each of these is being applied successfully at medical centers in a piecemeal manner. The andon cord is being implemented as a powerful patient safety tool, where healthcare workers at any level of the hierarchy can pull the cord and stop a procedure if they feel there is a threat to patient safety. Therefore, it can promote the safety culture of an institution and prevent catastrophes such as the wrong side being operated, wrong patient being operated from happening. However eliminating waste has not become part of the operational culture of medical centers. Just-in-time helps with preventing over ordering of expensive, time-sensitive medical implants and medications which will need to be discarded if not used within a certain time frame. With respect to jidoka, the hospital of today resembles that of a 100 years ago in every respect without many robotic employees. Humanoid robots (incidentally the biggest developers of which are Honda and Toyota) could potentially in the coming years take over many low-level functions which are currently expensive and highly labor intensive—such as basic nursing functions, helping debilitated, elderly patients walk without falling. The most important, immediate tools from TPS which can be applied in everyday medical care are Root Cause Analysis, kaizen, intelligent teamwork, and Plan-Do-Check-Act cycles. The application of just these three principles can have a significant impact on quality and dependability of healthcare.
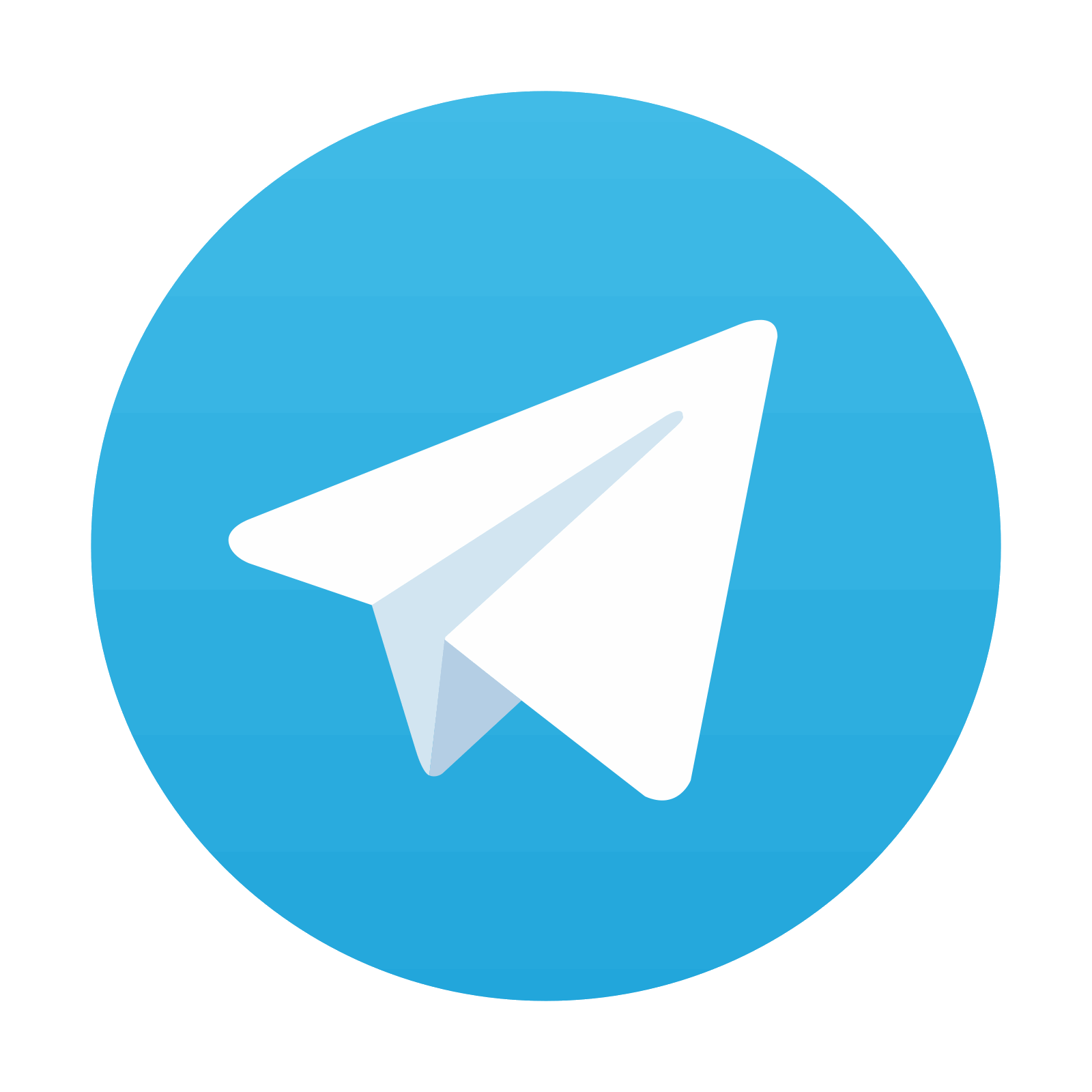
Stay updated, free articles. Join our Telegram channel
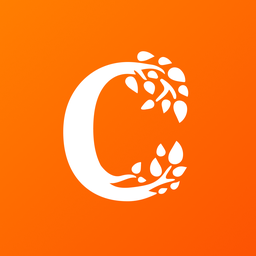
Full access? Get Clinical Tree
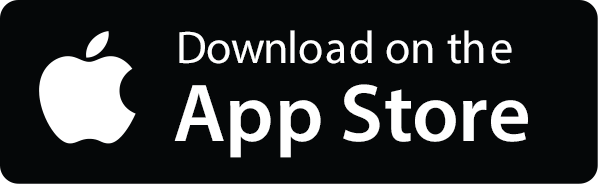
